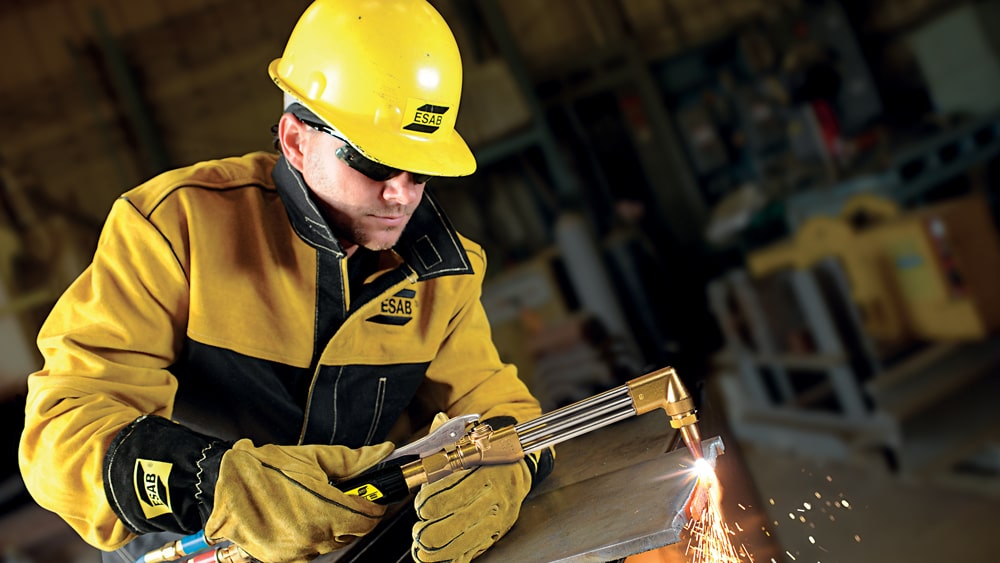
Welding is the backbone of the modern metalworking industry. Whether in a manufacturing unit or a repair workshop, you will usually find some type of welding machine everywhere.
There are many different methods of arc welding, including MIG, TIG, SAW and PAW. MIG welding is suitable for many applications and is particularly suitable for welding thick metal sheets and can also be used for very thick sections.
How does MIG welding work? And what is MIG welding used for?
In this article, we will introduce the MIG welding process and examine where and when to use it.
What is MIG Welding?
MIG definition: A welding process that fuses metals together using a consumable wire electrode shielded by an inert gas. The MIG welding process was developed in 1948 by The Battelle Memorial Institute and patented in 1949.
MIG welding is one of the two sub-types of Gas Metal Arc Welding (GMAW), the other being Metal Active Gas (MAG) Welding. The process and equipment are the same, the definition comes from the type of shielding gas used, for example, if inert argon gas is used as the shielding gas it is a MIG process. If active helium gas is used it is a MAG process. The choice of which type of shielding gas to use is determined by the metals to be welded.
What Metals Can Be MIG Welded?
MIG welding works for almost all metals, including (but not limited to) mild steel, stainless steel, aluminium, copper, magnesium, bronze and nickel. MIG welding is suitable for most metal thicknesses. However, it is usually not the preferred method for thin sheets because of the risk of burning through the sheet, although advances in the characteristics of modern MIG/MAG welding equipment have made this possible.
How MIG Welding Works – Process Characteristics
MIG welding is an arc welding process that uses a continuous solid wire electrode heated and fed into the weld pool from a welding gun. The two base materials are melted together forming a join. The gun feeds a shielding gas alongside the electrode helping protect the weld pool from airborne contaminants and keeps oxygen out of the molten metal.
In MIG welding, the operating works with a MIG welding torch, or ‘gun’. When the torch trigger is pressed:
- The torch starts to feed welding wire from a spooled wire feed unit.
- An electrical arc is created between the welding wire and workpiece, which heats the workpiece, melts the wire and fuses it to the joint area.
- The torch releases a shielding gas flow to shield the junction of the workpiece and the melted wire from a nozzle around the wire in the torch.
For a more detailed understanding, we will examine the key features of the MIG welding process.
Metal Transfer Mode
MIG welding works by using an arc to melt the base material and feed filler wire metal into it. The joint is formed as a mixture of the filler metal wire and the base metal.
The method by which the filler wire is transferred into the weld pool can be done in several different ways, the choice of which method to use is dependent on the position of the weld, (for example upside down,) and the type and thickness of the material being welded. The four most common transfer types are described here:
Short Circuit Mode or Dip Transfer
In short circuit or dip transfer mode, the speed of the wire feeding into the weld pool is increased so that it physically touches the weld pool. The short circuit melts the wire and deposits it in the weld pool. These short circuits can take place 20 – 200 times per second.
For the wire, either solid wire or solid-cored wire is used. It is a low voltage and low heat input welding method.
The short circuit method can be used in all positions, vertical up, vertical down, horizontal, or overhead. Typical shielding gas is 75%-85% argon.
Globular Mode
In globular mode, a continuous arc is maintained between the wire and the workpiece and the metal is transferred to the weld pool as droplets.
Creating these large drops of metal requires a high amount of heat. The diameter of the metal droplets is much greater than the diameter of the wire.
In globular mode, welding can be done at high speed but not for positional welding as the droplets fall into the weld pool by gravity. Typical shield gas is pure CO2, which makes it an inexpensive method. However, globular transfer can create a lot of spatter and looks unsightly so additional post-weld cleaning processes may be required.
Spray Mode
Unlike the short circuit and globular mode, the spray transfer mode occurs at a high voltage, typically >25V for a 1mm diameter wire. The wire feed speed is adjusted to give more than 250A and the welding arc burns continuously. Metal melts from the wire and passes across the arc in a series of small droplets, called spray transfer. This mode of transfer consists of a ‘spray’ of very small molten metal droplets which are projected towards the workpiece by electrical forces within the arc. The diameter of the droplets is typically 0.5 – 1 times the diameter of the electrode wire and the resulting weld bead is usually clean and aesthetically pleasing with low spatter. This mode of transfer is not suited to positional welding, although it can be used for positional welding of aluminium and its alloys.
Pulse Mode
Unlike the methods mentioned above, the pulse metal transfer mode requires dedicated MIG welding machines with pulse MIG functionality.
In its simplest form, this consists of a period at a background current that maintains the arc but does not achieve metal transfer, followed by a period of high current during which spray transfer occurs. The average current is midway between background and peak and can be well below the threshold normally associated with spray transfer. This means that the weld pool size is relatively small and positional welding is possible even though the transfer mechanism is spray. Pulsed MIG welding is all positional and produces clean weld beads with minimal spatter and a reduced heat-affected zone. It is suitable for thin or thick materials. The shielding gas for pulsed MIG is typically argon.
How MIG Welding Works – Components
Wire Electrode/Filler Metal
The welding wire acts as a consumable electrode that creates the arc. The wire serves as both the source of the heat, (via the arc at the contact tip) and filler metal for the joint and is fed through a copper tube called a contact tip, which conducts current into the wire. The choice of filler metal is dependent on the materials being joined, generally, the same type of metal grade will be used, for example, low alloy filler wires to join low alloy steels and stainless steel wires for stainless steel joints. Also, the mechanical and corrosion-resistant properties of the filler metal must match, or better still overmatch the properties of the base metal. If in doubt the manufacturers of both the base metal and the filler metal can advise on what they would recommend. Typical diameters of wire for MIG welding are from 0.8mm up to 1.6mm and again the choice is dependent on the joint configuration and thickness of the material.
Shielding Gas
The shielding gas isolates the weld pool from the atmosphere, so the molten metal does not oxidise. The shielding gases most commonly used are argon, helium, and carbon dioxide. Usually, a mixture of these gases is used instead of pure gases, with the ratio depending on the type of base metal, type of weld metal, and the mode of metal transfer.
Welding Torch
The MIG welding torch connects to the welding power source with a cable that carries the electrical current, welding wire and shielding gas. It has a trigger switch that turns on the electric arc, releases the shielding gas, and starts the wire feed at the same time. At the working end of the torch, a contact tip guides the wire and acts as a conductor for the welding arc between the torch and filler metal. This copper contact tip wears out through use and is a consumable that needs to be replaced after some hours of welding. The diameter of the hole in the contact tip is suited to the diameter of the wire going through it.
Power Source
Welding takes place at relatively low voltage compared with the input mains electricity and much higher current. Any variation in the arc length, that is the distance between the filler wire and the base metal, causes a change in the voltage. With the MIG welding process requiring the wire to be constantly fed into the weld pool then in order to ‘smooth’ this out the power supply for MIG welding is required to deliver a constant voltage to the torch. The selection of the power source is dependent upon the thickness of the base metal, the material type and the number of hours that the machine will be running in a day.
Advantages of MIG Welding
Advantages of MIG welding include:
Versatility
MIG welding is a highly versatile welding process, suitable for many different types, sizes and thicknesses of metals and in all welding positions.
Automation
MIG welding can readily be mechanised or fully automated. A high-speed robotic or semi-automatic setup offers faster MIG welding with more consistent results.
Weld Bead Aesthetics
MIG welding offers an attractive weld bead that does not ruin the appearance of the joints. There is minimal spatter and visible heat-affected zones. The finished MIG weld is visually appealing.
Disadvantages of MIG Welding
While MIG welding is a popular welding technique, the process has the same limitations as with all welding processes:
Burn Through
Burn through occurs when the base metal completely melts, and the molten metal of the weld falls through. There is a possibility of burn-through when MIG welding thin metals in globular or spray transfer modes. Short circuit transfer is more appropriate for thinner metals.
Lack of Fusion
Lack of fusion is a type of weld defect which occurs when the molten metal, the weld pool, does not completely fuse with the cold base metal and is more prevalent in thicker materials. For this reason, spray transfer mode is advised for MIG welding thicker materials.
Shielding Gas
For MIG welding that requires a higher percentage of argon, the overall cost of the welding process is increased since argon is one of the most expensive inert shielding gases. Also because of the requirement of a shielding gas for this process, it is not easy to use outside of the workshop. Any draughts will blow the shielding gas away from the end of the torch.
Positional Limitations
MIG Welding in globular and spray Transfer modes limits the weld position. You can only use these methods in a horizontal or flat position.
MIG Welding Applications
What is a MIG welder used for? MIG welding is the primary method for metal welding in industry, with more than 50% of the global welded metal done with a MIG welder.
MIG welding is common in the automotive industry where the all-positional properties of the process and the wire filler being fed from a spool lend itself to automation; the torch is attached to a robotic arm. Besides the automotive segment, many other industries that are fabricating sheet metal, pipes, thick section beams for construction, shipyards and general workshops also use the MIG welding process.
Conclusion
MIG welding is one of the most popular welding methods used by both amateurs and professionals. This is partly due to the benefits it offers and partly due to its ease of use.
While the technical feature of a MIG welding power-source can help improve your weld quality, the best way to improve your results is to practise your welding technique and optimise the settings for the metal and filler you are welding. For advice on the choice of power supply, filler wire, shielding gas and welding parameters ESAB have skilled welding engineers who can assist.
Using high-quality MIG welding equipment will make your job a lot easier. Check out ESAB’s range of industrial MIG welding equipment and high-quality filler metals and ensure you have the right tools for your job!